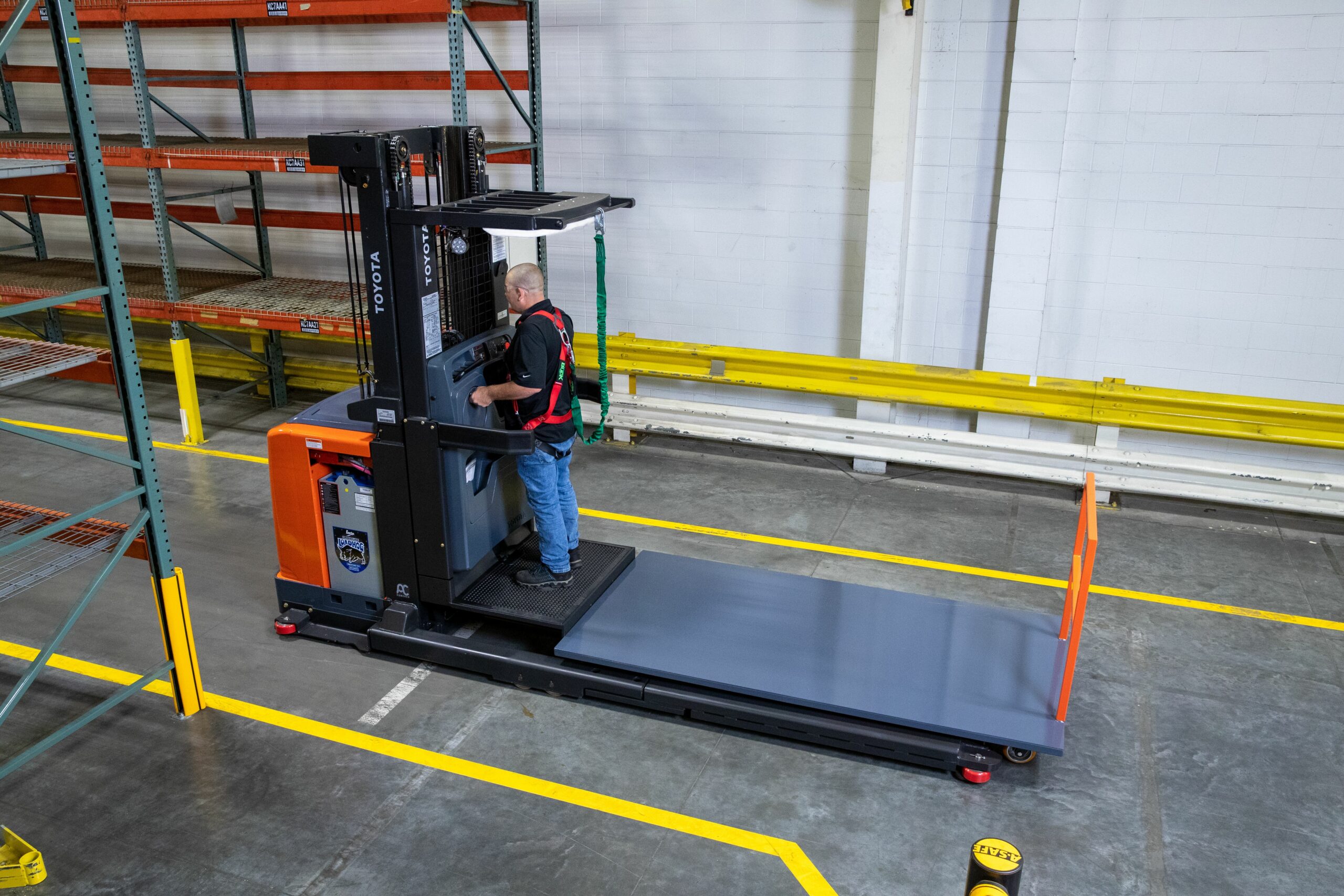
order picker platform
Order Picker Platform: Streamlining Warehouse Operations
Order picking, the process of selecting and preparing products for shipment, is a crucial component of any successful e-commerce or warehousing operation. A robust order picker platform plays a vital role in optimizing this process, boosting efficiency, and minimizing errors. This comprehensive guide delves into the intricacies of order picker platforms, exploring their functionalities, benefits, and best practices for implementation.
Introduction to Order Picker Platforms
Order picker platforms are automated systems designed to improve the efficiency and safety of order picking in warehouse settings. These platforms, whether electric, pneumatic or manual, move personnel and/or material around a warehouse to efficiently locate and retrieve goods. Understanding the specific needs of a facility will allow your company to effectively leverage order picker platform features and gain competitive advantages in today's logistics landscape.
What are the Key Components of an Order Picker Platform?
Different order picker platforms have varied configurations. However, common elements often include:
- Material Handling System: This includes conveyors, lifts, robots or a specialized workstation supporting order picking platform function. These systems are integrated to support effective flow in warehouse management and operational workflow using the order picker platform.
- Picking Technology: A crucial part of an order picker platform is integrating scanners, screens, and/or touch-screens for location finding, real-time inventory updates, and order verification. The order picker platform is more effective when these technologies are optimized for ease-of-use, providing the needed control and order visibility.
- Warehouse Management System (WMS): Many order picker platforms are closely tied to a WMS. The order picker platform must be integrated seamlessly with the system so the right product information is routed correctly to the platform.
- Ergonomics & Safety Features: A well-designed order picker platform prioritizes operator safety, ergonomic features, and proper lift height to ensure a fatigue-free experience, impacting the user's comfort level and their ability to make good decisions related to picking process using the order picker platform..
How to Choose the Right Order Picker Platform for Your Business
Source: lifttrucksupplyinc.com
Evaluating an order picker platform often requires careful consideration:
-
Warehouse Layout: Assess your warehouse space. Is your warehouse optimized to incorporate a suitable order picker platform solution? Does your current layout necessitate custom-built features from the order picker platform system to ensure optimized integration?
-
Order Volume: How many orders do you handle per day or week? This influences your need for automation, with high order volumes requiring specialized automated order picker platform implementations to handle pick demands.
-
Product Characteristics: Determine the types and sizes of the products being picked. Some order picker platforms excel in certain conditions; different orders need distinct platforms for support and operation with your current order picker platform.
Understanding Order Picking Process Efficiency Improvements
How an order picker platform enhances operational performance can be measured through these key indicators:
-
Reduced Picking Time: The order picker platform enables picking personnel to concentrate on the task of order completion, streamlining the picking process to reduce overall processing time, thereby ensuring goods move faster from pick zone to shipping zone using the order picker platform.
-
Reduced Errors: Automated systems, using advanced integrations on the order picker platform, minimize human errors, further bolstering order fulfillment accuracy.
Maximizing Order Picker Platform Productivity
How does one ensure maximum productivity from their order picker platform investment?
-
Employee Training: Order picker platforms are crucial to efficiently process items from one part of the facility to the other in order fulfillment operations. Comprehensive training programs enhance the order picker platform’s usability. Trained operators proficient in using the order picker platform will lead to significantly reduced downtime and a more efficient warehouse operation.
-
Integration Strategy: Careful integration between the order picker platform and the company's wider warehouse management system (WMS) guarantees the accuracy, effectiveness, and security of order picking workflow processes with the chosen order picker platform.
Maintaining Optimal Order Picker Platform Functionality
Source: midlandpallettrucks.com
Maintaining order picker platforms is an important function. Keeping track of this system's integrity through ongoing upkeep ensures the platform functions properly for a variety of tasks.
-
Routine Inspections: Consistent inspections and scheduled preventative maintenance enhance the life expectancy and uptime of an order picker platform.
-
Regular Upgrades: In today's evolving logistics world, ongoing order picker platform upgrades or improvements for newer software, hardware or improved equipment allow an organization to maintain peak operating efficiency. Always keep the chosen order picker platform current to its best form by regularly applying available updates.
Safety Considerations for Order Picker Platforms
Source: hubtex.com
Implementing an order picker platform includes stringent safety considerations, such as
-
Operator Training: Thorough operator training programs will address procedures for safe operation, avoiding injury to users and reducing facility liabilities while operating order picker platforms safely.
-
Compliance Requirements: Ensuring proper certification and alignment with established regulatory guidelines for order picker platform and related safety equipment is a key component to avoid accidents.
FAQs About Order Picker Platforms
Here are a few frequent questions about order picker platforms:
Q: What is the ROI of implementing an order picker platform?
A: The ROI depends on factors like order volume, current inefficiencies, and platform investment costs. Implementing an order picker platform can produce significant gains through faster order processing times, reduced error rates, and streamlined operations; improved profitability will follow once those are realized by using the new order picker platform.
Q: What is the difference between different order picker platforms on the market?
A: Variations in order picker platforms encompass differing sizes, configurations (electric, pneumatic), automated features, capacity limitations and ergonomic features specific to each platform for user safety and comfort; therefore these features influence usability and productivity rates that differ across specific order picker platforms on the market. Features of an order picker platform determine the differences.
Conclusion
Source: com.au
An effective order picker platform significantly enhances operational efficiency, optimizes resource allocation and significantly improves the bottom line of any warehouse operations through increased productivity from its selected order picker platform, ensuring cost-effective and efficient fulfillment procedures, by incorporating safety practices that maintain operational control within a streamlined warehouse facility leveraging advanced automation.
Source: materialhandlingsolutions.com
Future Trends in Order Picker Platforms
Advanced trends impacting the evolution of order picker platforms often involve automated guidance systems, integrated artificial intelligence features to increase picker speed and further minimize error potential on the order picker platform, enhanced connectivity capabilities for seamless integration of diverse operations with their chosen order picker platform solution and integration into an ecosystem to increase scalability.